What is it?
The original Torq construction – a whole new way to build surfboards.
First we blow a blank to the exact finished size with a measured weight of EPS. We don’t hand shape or CNC these, they are made perfect first time – perfect shape, perfect weight, perfect foam structure.
The blank is covered in Biaxial fiberglass cloth and our unique Shield Skin with a computer mixed and measured volume of epoxy resin.
A second press mold – precision CNC cut from a single block of aluminium – is used to cure the resin, heated for perfect resin distribution.
What’s the benefits?
Accuracy – there’s no shaping, sanding and guess work. The whole process is controlled; foam density, resin content, fin inserts.
Low waste – no shaping means no shaping waste. The cloth is laid up dry so off-cuts can be recycled. Resin is measured by weight and applied with no waste dripping on the floor.
Durability – Biaxial cloth is stronger than plain weave and we can use a lot due to the efficient lay-up. Our blanks use high density EPS and epoxy resin is stronger than Polyester.
Sustainable – A low waste process and a long lifespan = less impact. The production is run on solar power. All materials are sourced locally. Shipping is in slim fit, bleach free boxes with plastic free packing. We make the fin boxes from GRS and UL certified recycled plastic.
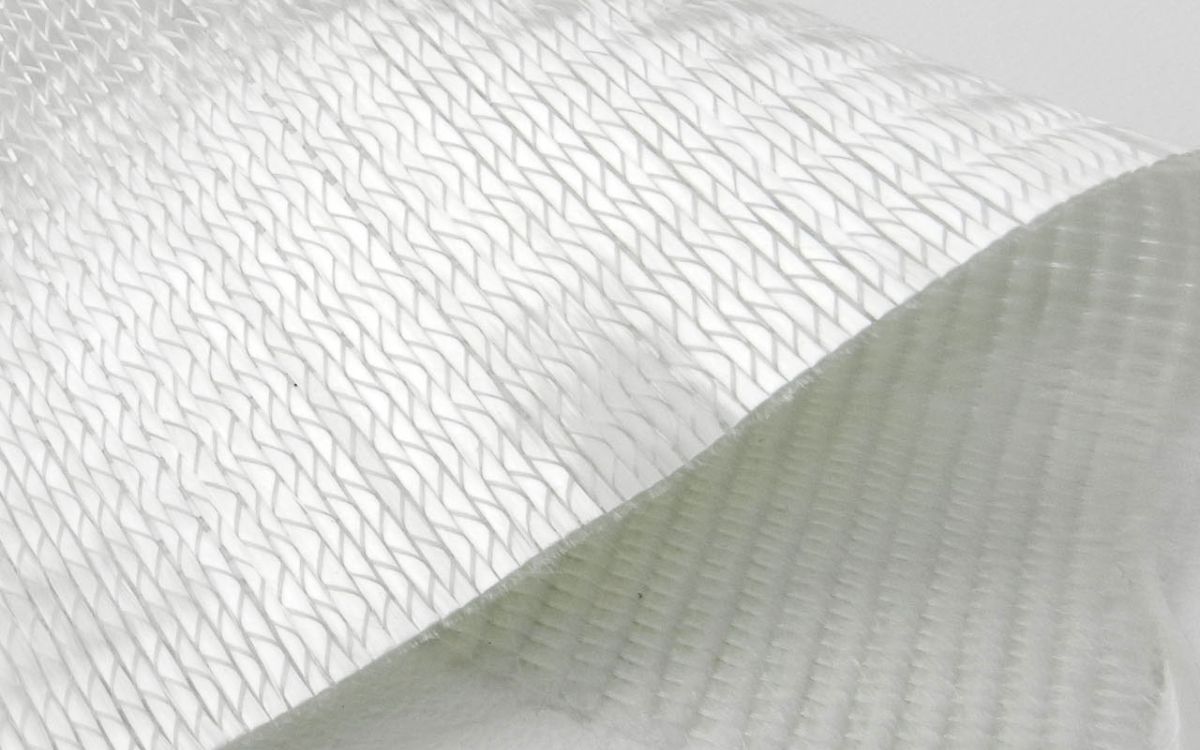
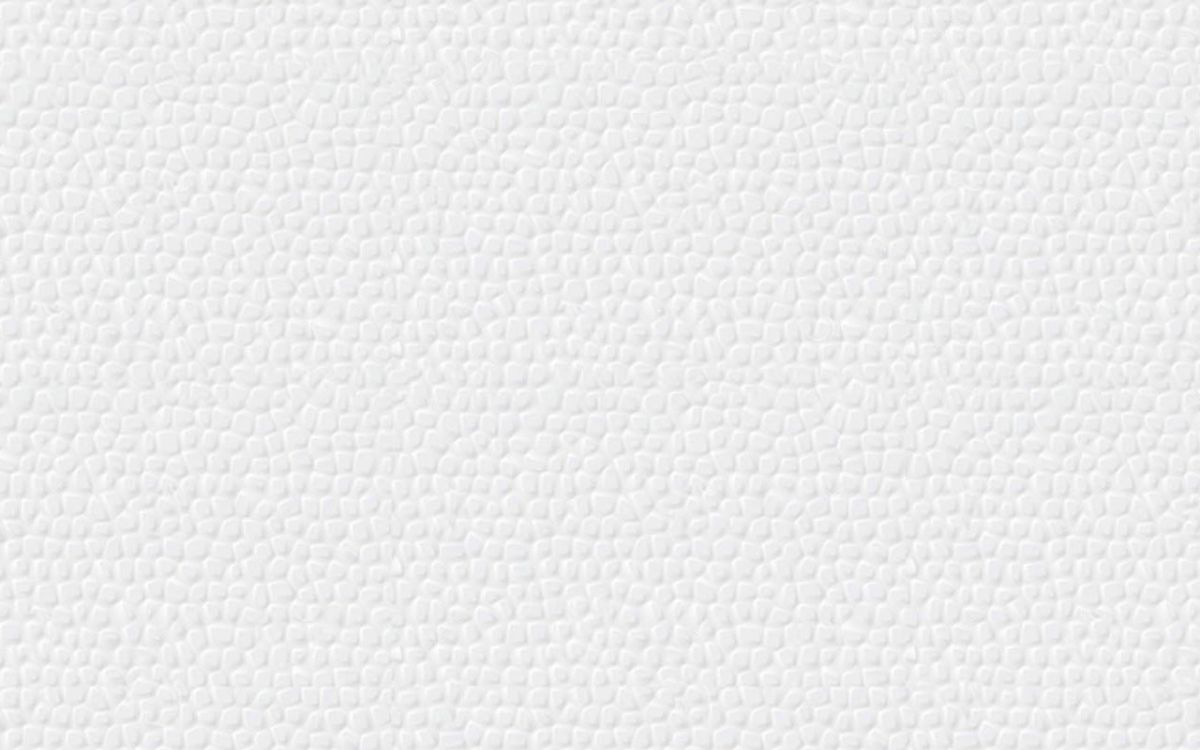
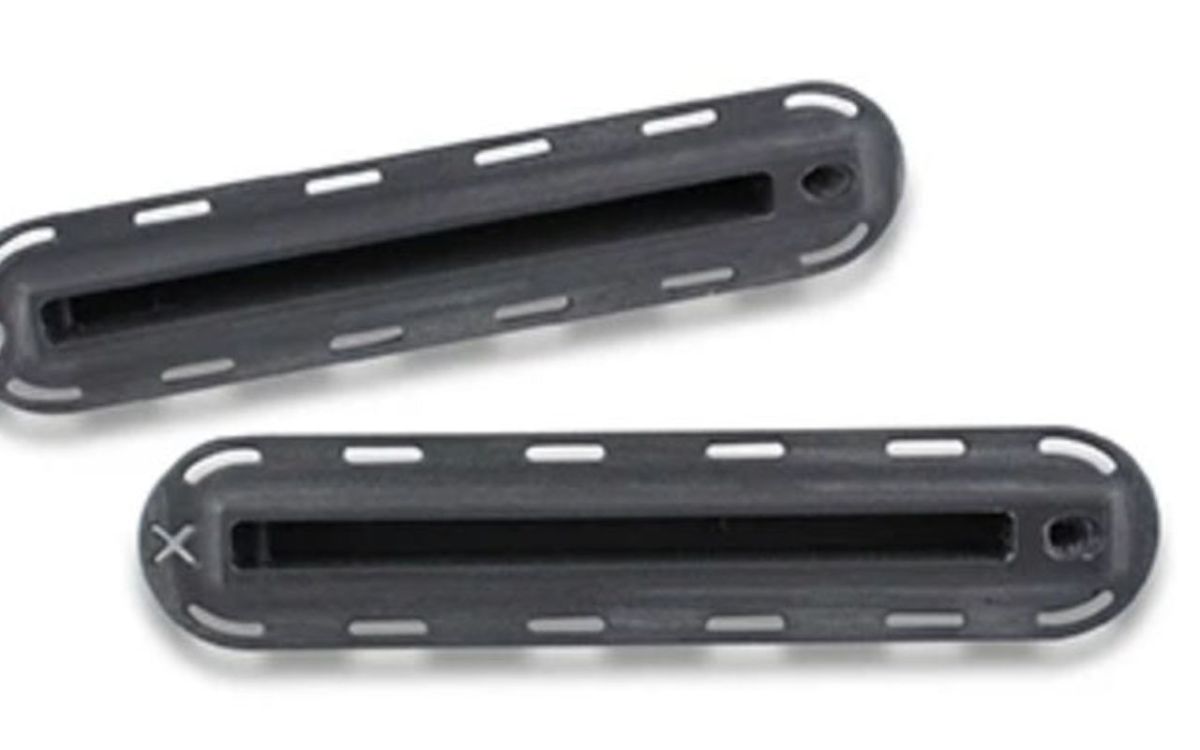
How do they surf?
The feel is similar to PU. The extra fiberglass means they absorb chatter well, without the super lightweight response of the TEC. They have a nice light neutral feel – responsive but forgiving.

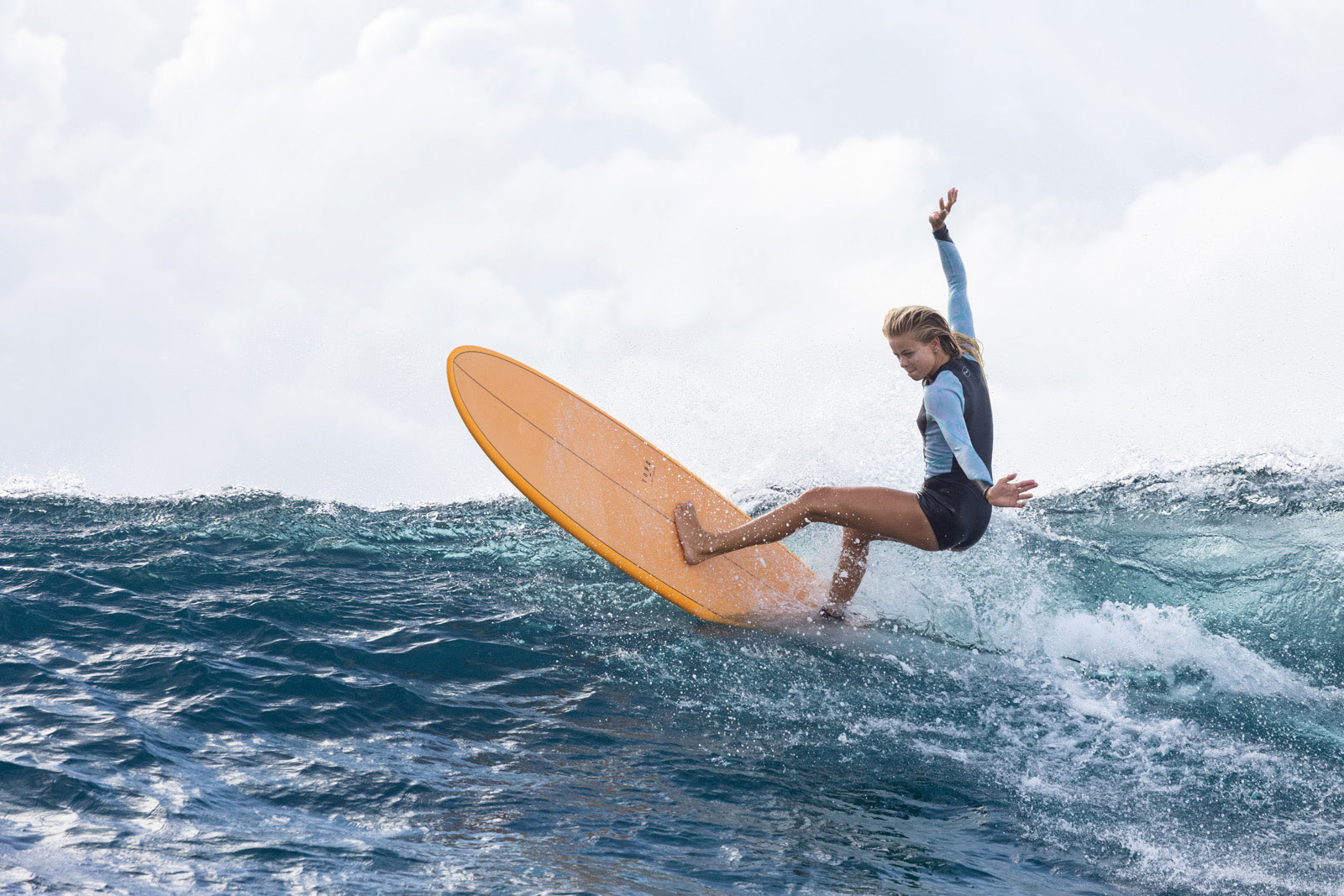