Torq Sustainability
The torq brand was founded on a new and revolutionary way of producing surfboards with perfect accuracy and nearly no waste. From Day One we aimed to make Torq surfboards the most efficient, leanest, low waste product that we can.
Ultimately surfboards are a mixed material product that’s currently not recyclable or biodegradable and every board purchased has an impact in production and end of life. To claim sustainability or eco credentials can be extremely misleading if not properly explained and supported, with an overview of the full impact of the products lifespan, not isolating one part.
LOW WASTE PRODUCTION:
We make our boards differently to everyone else.
The original Torq surfboard – the TET, now also TET-CS and X-Lite – was designed around a new system of making surfboards. An EPS blank is blown in a mold with no shaping waste, then wrapped in Biaxial cloth, the offcuts removed while dry and recycled with other glass recycling. The resin is measured by computer and applied in a molding system with no waste resin. The molded board requires minimal finishing – no extensive sanding or cleaning of auxiliaries like brushes and squeegees with acetone or cellulose.
The power for our molding process comes from solar power with a 700kw solar installation on our production site.
This is the cleanest, lowest waste process currently used in surfboard making. Check our process sheets on the technology pages for full info.
![]() |
LOCALLY SOURCEDOur blanks are made nearby the TET production. Fins and fin boxes are also made nearby (using a Futures Fin approved mold), resin is sourced within 100km. |
![]() |
RECYCLEDUnlike traditional methods where the resin and cloth are combined before removing the excess, thereby creating a non-recyclable waste, our glass fiber cloth is laid up dry and the excess is removed before resin is applied. The excess cloth is recycled as normal glass recycling. Our fin boxes in TET and X-Lite are made from recycled plastics |
![]() |
RENEWABLE ENERGYThe power for our molding process comes from solar power with a 700kw solar installation on our production site. |
QUALITY MATERIALS:

Biaxial glass fiber
Non woven bi-directional cloth has extremely high strength and torsional stiffness making our TET, TET-CS and X-Lite boards some of the strongest available.
Our unique lay-up and molding process means the off-cuts can be recycled.

Plain Weave Fiber
On TEC and ACT we use a standard plain weave fiber, but we use a lot more of it; industry standard lay-ups are usually 2 x 4oz or 4oz + 6oz on the deck and a single 4oz or 6oz on the base. We use an extra 6oz deck patch and an extra 4oz or 6oz on the base ie. double the amount of fiber.

Carbon Fiber
In TET-CS, X-Lite, TEC and ACT we use a Uni-Directional Carbon Fiber. This is non woven and therefore stronger than carbon weave.
This is genuine carbon strands, not just tape or paper transfers as sometimes used for aesthetics. This gives the boards more stiffness and strength.
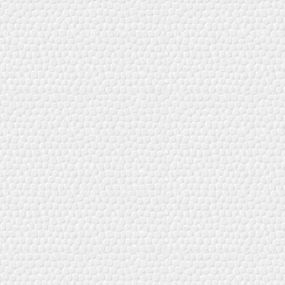
EPS Foam
We only make surfboards with EPS foam and Epoxy resin.
Our EPS is high density model blown, using only steam to expand the beads and blow the blank. This is far better than Polyurethane foam which releases toxic MDI and TDI in the blank blowing process.
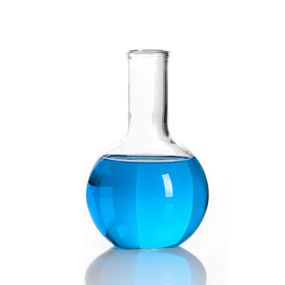
Epoxy Resin
Stronger than Polyester resin and with significantly less VOC’s (Volatile Organic Compounds).
We are testing bio-based resin to get the best balance of low waste production and durability.

Components
We produce Futures finboxes under license for our molded boards to avoid shipping. We use GRS and UL certified recycled plastic.
WE MAKE STRONG BOARDS
The most overlooked and under marketed part of sustainability in surfboards is durability. A lightweight board with only a few layers of 4oz cloth is landfill waiting to happen. The most sustainable surfboard is the one that lasts the longest.
We’ve tested some of our technologies for over a decade and any new tech is throroughly tested by ourselves and our team.
All of our boards are rated for strength on our Tech Compass, shown on our website for each board.
DURABILITY/LOW WASTE EFFECT
The combination of durability AND low waste is critical to overall sustainability.
With each new board comes a footprint; material waste, energy usage and ultimately the board itself. A weak board that’s replaced each year multiplies the total footprint, whereas a board with durability AND low waste has a much lower impact over time.
LOW IMPACT SHIPPING
Shipping is a 2-sided issue. A surfboard maker will need to ship all of the component parts – blanks, fiberglass, resin, leash cups, fin boxes, as well as brushes, squeegees, sanding auxiliaries, cleaning chemicals etc. And then ship the finished board to the shop or customer.
Our production is positioned close to all suppliers, and in some cases we make the parts ourselves, so we only need to ship the finished product, not the unfinished parts. And our low waste process means we’re not shipping the waste element with the raw materials.
Our boards are wrapped in plastic free packaging using paper and gumtape and shipped in slim fit, bleach free cardboard boxes.